NEETS Module 15 - Principles of Synchros, Servos, and Gyros
Pages i,
1-1,
1-11,
1-21,
1-31,
1-41,
1-51,
1-61,
1-71,
2-1,
2-11,
2-21,
2-31,
3-1,
3-11,
3-21,
4-1, Index
Some synchro systems contain a differential and a control transformer, as illustrated in figure 1-32. In this
figure, there are large stator currents flowing in the CX, since it supplies all the losses as well as the
magnetizing current for both synchros.

Figure 1-31. - The use of a synchro capacitor with a TDX.
Two meters are placed in the circuit to show the value of stator current
for the CDX and CT. Another meter is placed in series with the ac excitation voltage to show the amount of current
being drawn from the ac line is 0.9 ampere.

Figure 1-32. - Synchro current in a control synchro system using a CDX and a CT.
Adding synchro capacitors to this system, as shown in figure 1-33, greatly reduces the stator currents and
improves the efficiency of the system. Also, notice that the line current is reduced from 0.9 ampere in figure
1-32 to 0.65 ampere in figure 1-33.

Figure 1-33. - The effects of synchro capacitors in a control synchro system using a CDX and a CT.
1-41
When a synchro capacitor is used, it is always placed physically close to the differential or control
transformer whose current it corrects. This is done to keep the connections as short as possible, because high
currents in long leads increase the transmitter load and reduce the accuracy of the system. We must stress
that the synchro capacitor should never be used in a simple transmitter-receiver system. This is because stator
currents in this system are zero at correspondence and the addition of a synchro capacitor would only increase the
stator current and throw the system out of balance. Q-48. What is the purpose of the synchro
capacitor?
Q-49. What type of synchros usually require the use of synchro capacitors? Q-50.
What type of current is eliminated by synchro capacitors? Q-51. How are synchro capacitors
connected in a circuit? Q-52. Why are synchro capacitors placed physically close to
differentials transmitters and CTs?
MULTIsPEED SYNCHRO Systems
The data to be transmitted is another important factor that we must consider when we discuss the accuracy of a
synchro system. If this data covers a wide range of values, the basic synchro system is unable to detect any small
changes in the data. When this happens, the accuracy of the system decreases. Because of this difficulty,
multispeed synchro systems were developed. They handle this type of data very effectively and still maintain a
high degree of accuracy. Multispeed synchro systems use more than one speed of data transmission. The
speed of data transmission is, simply, the number of times a synchro transmitter rotor must turn to transmit a
full range of values. For example, a system in which the rotors of synchro devices turn in unison with their input
and output shafts is commonly called a 1-speed data transmission system. In this system, the transmitter's rotor
is geared so that 1 revolution of the rotor corresponds to 1 revolution of the input. Until now, the discussion of
synchro systems has dealt exclusively with this 1-speed system. In a 36-speed data transmission system,
the rotor of the synchro transmitter is geared to turn through 36 revolutions for 1 revolution of its input. Units
transmitting data at one speed are frequently called 1- speed synchros; a unit transmitting data at 36-speed would
be a 36-speed synchro, and so forth.
It is quite common in synchro systems to transmit the same data at two different speeds. For example, ship's
course information is usually transmitted to other locations on a ship at 1-speed and 36- speed. a system in which
data is transmitted at two different speeds is called a dual- or double-speed system. Sometimes a dual-speed
system will be referred to by the speeds involved, for example a 1- and 36-speed system. In summary, the
speed of data transmission is referred to as 1-speed, 2-speed, 36-speed, or some other definite numerical ratio.
To indicate the number of different speeds at which data is transmitted, refer to the system as being a
single-speed, dual-speed, or tri-speed synchro system. Single-SPEED SYNCHRO System
If the data to be transmitted covers only a small range of values, a single-speed system is normally accurate
enough. However, in applications where the data covers a wide range of values and the accuracy of the system is
most important, the 1-speed system is not adequate enough and must be replaced by a
1-42
more suitable system. Increasing the speed of a single-speed system from 1-speed to 36-speed provides
greater accuracy, but the self-synchronous feature of the 1-speed system is lost. If primary power is interrupted
in a 36-speed system and the transmitter is turned before power is reapplied, the synchros could realign
themselves in an erroneous position. The number of positions in which the transmitter and receiver rotors can
correspond is the same as the transmission speed. Thus, in the 36-speed system, there are 35 incorrect positions
and only 1 correct position of correspondence.
For accurate transmission of data over a wide range of values without the loss of self-synchronous operation,
multispeed synchro systems must be used. Multispeed synchro systems use more than one speed of data transmission
and, therefore, require more than one output shaft.
DUAL-SPEED SYNCHRO System A basic dual-speed synchro system consists of two
transmitters and two receivers, as shown in figure 1-34. One transmitter receives the external input to the system
and, through a network of gears, passes the effects of the external input to the second transmitter. The gear
ratio between these two transmitters determines the two specific speeds the system will use to transmit the input
data. The two speeds of this system are often referred to as fast and slow, high and low, or more often as fine
and coarse.
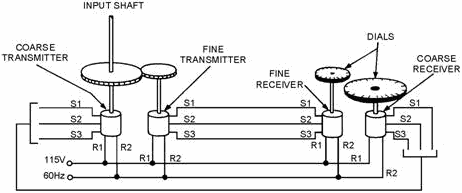
Figure 1-34. - Dual-speed synchro system.
If, for example, the gear ratio between the two transmitters is 36 to 1, 1 revolution of the rotor of the first
transmitter causes 36 revolutions of the rotor of the second transmitter. The first transmitter-the one that
accepts the external input-can be called the coarse transmitter, and the second one can be called the fine
transmitter. Representative speeds include 1 and 36, 2 and 36, and 2 and 72. The output of each
transmitter is passed through standard synchro connections to a receiver. One receiver receives the coarse signal
and the other one receives the fine signal. The two receivers may or may not be connected by a network of gears
similar to the network between the two transmitters. In some dual-speed applications, a double receiver is used
instead of two individual receivers. The double receiver (fig. 1-35) consists of a coarse and a fine
receiver enclosed in a common housing. It has a two-shaft output one inside the other. The coarse and fine
receivers may be likened to the hour and minute hands of a clock. The coarse receiver corresponds to the hour
hand, and the fine
1-43
receiver corresponds to the minute hand. This double receiver has the advantage of requiring less space
than two single receivers. However, it also has a disadvantage - when one receiver goes bad, both must be
replaced.
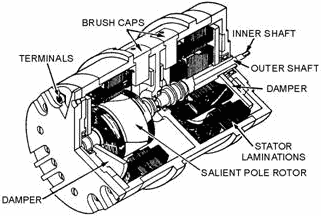
Figure 1-35. - Cutaway view of a double receiver.
In the dual-speed synchro system, data is transmitted by the coarse transmitter, while the system is far out of
correspondence and then is shifted to the fine transmitter as the system approaches correspondence. This shifting
from coarse to fine control is done automatically when the fine error signal exceeds the coarse error signal. The
fine synchro transmitter then drives the system to the point of correspondence. When the dual-speed
synchro system includes control transformers, there is always the possibility of a 180º error being present in the
system. The reason is the rotor of the CT is not energized and its error- voltage output is zero both at its
proper position and also at a point 180º away from that position. To prevent the CT from locking 180º out of phase
with the rest of the system, a low voltage is applied across the rotor terminals of the coarse CT as shown in
figure 1-36.
1-44
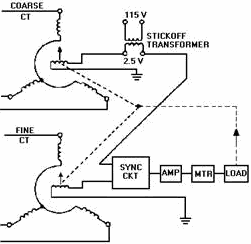
Figure 1-36. - Dual-speed synchro system using a stickoff transformer.
This voltage is normally about 2.5 volts and is commonly termed "stickoff" voltage. It is obtained from the
secondary of a small transformer. The voltage induced in the secondary of the transformer shifts the 0º position
of the coarse CT To reestablish a new 0º position, the stator of the coarse CT must be turned through an angle
that induces an opposing 2.5 volts in the rotor to cancel the stickoff voltage. Therefore, at 0º the two voltages
cancel and no input exists to drive the servo amplifier. Should the rotor of the CT stop at 180º, the same 2.5
volts would be induced in the rotor. However, it would be in phase with the stickoff voltage and no cancellation
would occur. The end result is an error signal at 180º that drives the dual-speed synchro system out of any false
synchronizations.
TRI-SPEED SYNCHRO System The advent of long-range missiles and high-speed aircraft has
brought about the need for accurately transmitting very large quantities. This is best done by a tri-speed synchro
system, which transmits data at three different speeds. These speeds are sometimes referred to as coarse, medium
or intermediate, and fine. a typical weapons systems, for example, might transmit range in miles, thousands of
yards, and hundreds of yards. By providing this range in three different scales, greater accuracy is obtained than
would be possible with a dual-speed system. Representative speeds for tri-speed systems include 1, 36, and 180; 1,
36, and 360; and 1, 18, and 648. Q-53. What is the name given to the synchro system that
transmits data at two different speeds? Q-54. What is the main reason for using a multispeed
synchro system instead of a single-speed synchro system? Q-55. In a dual-speed synchro system
what determines the two specific speeds at which the data will be transmitted? Q-56. What type
of synchro system is used to transmit very large quantities?
1-45
Q-57. What is the disadvantage of using a double receiver instead of two individual
receivers? Q-58. What is the purpose of "stickoff voltage"?
ZEROING SYNCHROS
If synchros are to work properly in a system, they must be connected and aligned correctly with respect to each
other and to the other devices with which they are used. The reference point for alignment of all synchro units is
ELECTRICAL ZERO. The mechanical reference point for the units connected to the synchros depends upon the
particular application of the synchro system. Whatever the application, the electrical and mechanical reference
points must be aligned with each other. The mechanical position is usually set first, and then the synchro device
is aligned to electrical zero. There are various methods for zeroing synchros. Some of the more common
zeroing methods are the voltmeter, the electrical-lock, and the synchro-tester methods. The method used depends
upon the facilities and tools available and how the synchros are connected in the system. Also, the method for
zeroing a unit whose rotor or stator is not free to turn may differ from the procedure for zeroing a similar unit
whose rotor or stator is free to turn.
VOLTMETER METHOD The most accurate method of zeroing a synchro is the ac voltmeter
method. The procedure and the test circuit configuration for this method vary somewhat, depending upon which type
of synchro is to be zeroed. Transmitters and receivers, differentials, and control transformers each require
different test circuit configurations. Regardless of the synchro to be zeroed, there are two major steps
in each procedure. The first step is the coarse or approximate setting. The second step is the fine setting. The
coarse setting ensures the device is zeroed on the 0º position rather than the 180º position. Many synchro units
are marked in such a manner that the coarse setting may be approximated physically by aligning two marks on the
synchro. On standard synchros, this setting is indicated by an arrow stamped on the frame and a line marked on the
shaft, as shown in figure 1-37. The fine setting is where the synchro is precisely set on 0º.
1-46
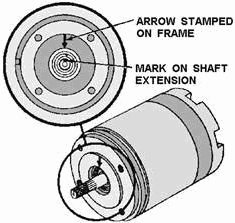
Figure 1-37. - Coarse electrical zero markings.
For the ac voltmeter method to be as accurate as possible, an electronic or precision voltmeter having 0- to
250-volt and a 0- to 5-volt ranges should be used. On the low scale this meter should also be able to measure
voltages as low as 0.1 volt. Q-59. What is the reference point for alignment of all synchro units?
Q-60. What is the most accurate method of zeroing a synchro? Q-61. What is the
purpose of the coarse setting of a synchro? Zeroing Transmitters and Receivers (Voltmeter Method)
Since the TX, CX, and TR are functionally and physically similar, they can be zeroed in the same manner. For the
TX and CX to be properly zeroed, electrical zero voltages (S2 = 52V; S1 and S3 = 26V) must exist across the stator
winding when the rotor of the transmitter is set to 0º or its mechanical reference position. The synchro receiver
(TR) is properly zeroed when the device it actuates assumes its zero or mechanical reference position while
electrical zero voltages (S2 = 52V; S1 and S3 = 26V) exist across its stator windings. The following is a
step-by-step procedure used to zero the TX, CX, and TR. 1. Carefully set the unit (antenna, gun
mount, director, etc.) whose position the CX or TX transmits, accurately on 0º or on its reference position. In
the case of the TR, deenergize the circuit and disconnect the stator leads before setting its rotor on zero or to
its reference position. The rotor may need to be secured in this position; taping the dial to the frame is usually
sufficient. 2. Deenergize the synchro circuit and disconnect the stator leads. Note: Many synchro
systems are energized by individual switches. Therefore, be sure that the synchro power is off before working on
the connections.Set the voltmeter to its 0- to 250-volt scale and connect it into the circuit as shown in view a
of figure 1-38.
1-47
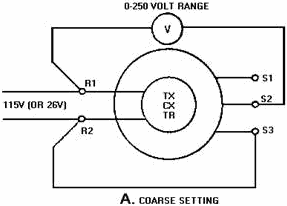
Figure 1-38A. - Zeroing a transmitter or receiver by the voltmeter method.
3. Energize the synchro circuit and turn the stator until the meter reads about 37 volts (15 volts for a
26-volt synchro). Should the voltmeter read approximately 193 volts (115 volts + 78 volts = 193 volts), the rotor
is at 180º. Turn it through a half revolution to bring it back to 0º. If you cannot obtain the desired 37 (or 15)
volts, use the lowest reading you can take with the meter. This is the coarse setting and places the synchro
approximately on electrical zero. 4. Deenergize the synchro circuit and connect the meter as shown
in view B. Start with a high scale on the meter and work down to the 0- to 5-volt scale to protect the meter
movement.
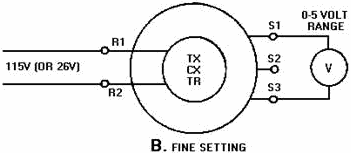
Figure 1-38B. - Zeroing a transmitter or receiver by the voltmeter method.
5. Reenergize the synchro circuit and adjust the stator for a zero or minimum voltage reading. This is
the fine electrical zero position of the synchro. When you have reconnected a TX and a TR into a system
after zeroing them, you can perform a simple check on the system to see if they are accurately on electrical zero.
First, place the transmitter on 0º. When the system reaches the point of correspondence, the induced voltages in
the S1 and S3 stator windings of both synchros should be equal. Since the terminals of S1 and S3 are at equal
potential, a
1-48
jumper between these terminals at the TR should not affect the circuit. If, however, the TR rotor moves
when you connect a jumper, there is a slight voltage difference between S1 and S3. This voltage difference
indicates that the transmitter is not on electrical zero. If this is the case, recheck the transmitter for
electrical zero.
Zeroing Differential Synchros (Voltmeter Method) A differential synchro is zeroed when it
can be inserted into a system without introducing any change. If a differential synchro requires zeroing, use the
following voltmeter method: 1. Carefully and accurately set the unit whose position the CDX or TDX
transmits on zero or on its reference position. In the case of the TDR, deenergize the circuit and disconnect all
leads before setting its rotor to 0º or to its reference position. You may need to secure the rotor in this
position; taping the dial to the frame is usually sufficient. 2. Deenergize the circuit and
disconnect all leads on the differential except leads S2 and S3 when you use the 78-volt (10.2 volts for 26-volt
units) supply from the transmitting unit to zero the differential. Set the voltmeter to its 0- to 250-volt scale
and connect it as shown in view a of figure 1-39. If the 78-volts is not available from the transmitter or from an
auto transformer, you may use a 115-volt source instead. If you use 115 volts instead of 78 volts, do not leave
the synchro connected for more than 2 minutes or it will overheat and may become permanently damaged.

Figure 1-39A. - Zeroing differential synchros by the voltmeter method.
1-49
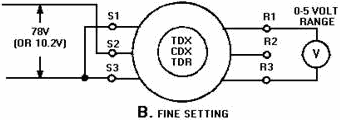
Figure 1-39B. - Zeroing differential synchros by the voltmeter method.
3. Energize the circuit, unclamp the differential's stator, and turn it until the meter reads
minimum. The differential is now approximately on electrical zero. Deenergize the circuit and reconnect it as
shown in view B. 4. Reenergize the circuit. Start with a high scale on the meter and work down
to the 0- to 5-volt scale to protect the meter movement. At the same time, turn the differential's stator until
you obtain a zero or minimum voltage reading. Clamp the differential stator in position, ensuring the voltage
reading does not change. This is the fine electrical zero position of the differential. Zeroing a
Control Transformer (Voltmeter Method) Two conditions must exist for a control transformer (CT)
to be on electrical zero. First, its rotor voltage must be minimum when electrical zero voltages (S2 = 52 volts;
S1 and S3 = 26 volts) are applied to its stator. Second, turning the shaft of the CT slightly counterclockwise
should produce a voltage across its rotor in phase with the rotor voltage of the CX or TX supplying excitation to
its stator. To zero a CT (using 78 volts from its transmitter) by the voltmeter method, use the following
procedure: 1. Set the mechanism that drives the CT rotor to zero or to its reference position. Also,
set the transmitter (CX or TX) that is connected to the CT to zero or its reference position. 2.
Check to ensure there is zero volts between S1 and S3 and 78 volts between S2 and S3. If you cannot obtain these
voltages, you will need to rezero the transmitter. Note: If you cannot use the 78 volts from the transmitter
circuit and, an auto transformer is not available, you may use a 115- volt source. If you use 115 volts instead of
78 volts, do not energize the CT for more than 2 minutes because it will overheat and may become permanently
damaged. 3. Deenergize the circuit and connect the circuit as shown in view a of figure 1-40. To
obtain the 78 volts required to zero the CT, leave the S1 lead on, disconnect the S3 lead on the CT, and put the
S2 lead (from the CX) on S3. This is necessary since 78 volts exists only between S1 and S2 or S2 and S3 on a
properly zeroed CX. Now energize the circuit and turn the stator of the CT to obtain a minimum reading on the
250-volt scale. This is the coarse or approximate zero setting of the CT.
1-50
- |
Matter, Energy,
and Direct Current |
- |
Alternating Current and Transformers |
- |
Circuit Protection, Control, and Measurement |
- |
Electrical Conductors, Wiring Techniques,
and Schematic Reading |
- |
Generators and Motors |
- |
Electronic Emission, Tubes, and Power Supplies |
- |
Solid-State Devices and Power Supplies |
- |
Amplifiers |
- |
Wave-Generation and Wave-Shaping Circuits |
- |
Wave Propagation, Transmission Lines, and
Antennas |
- |
Microwave Principles |
- |
Modulation Principles |
- |
Introduction to Number Systems and Logic Circuits |
- |
- Introduction to Microelectronics |
- |
Principles of Synchros, Servos, and Gyros |
- |
Introduction to Test Equipment |
- |
Radio-Frequency Communications Principles |
- |
Radar Principles |
- |
The Technician's Handbook, Master Glossary |
- |
Test Methods and Practices |
- |
Introduction to Digital Computers |
- |
Magnetic Recording |
- |
Introduction to Fiber Optics |
Note: Navy Electricity and Electronics Training
Series (NEETS) content is U.S. Navy property in the public domain. |
|