August 1960 Radio-Electronics
[Table of Contents]
Wax nostalgic about and learn from the history of early electronics.
See articles from Radio-Electronics,
published 1930-1988. All copyrights hereby acknowledged.
|
This "Introduction to Ultrasonics"
article from a 1960 issue of Radio−Electronics magazine does not necessarily
directly apply to RF and microwaves, but there are similarities in the circuitry
and theory of generation and propagation. I was surprised to learn that ultrasonics
even back then went into the low GHz realm. Any mechanical vibrations about about
20 kHz are regarded as ultrasonic. Ultrasonics can perform some of the functions
of x-rays in material inspection, without the danger of ionizing radiation and extremely
high voltages required to generate the rays. While working in the 1980's as an electronics
technician at the Westinghouse Oceanic Division in Annapolis, Maryland, I often
used an ultrasonic cleaner like the one shown here for removing flux from printed
circuit board assemblies (PCA's), cable connectors, and other objects. The heated
methyl-based bath solution produced a PCA with shiny solder joint totally devoid
of flux residue. We were still using 60/40, Sn/Pb rosin core solder back then. We
built sonar systems and components for the U.S. Navy, including transducer-equipped
torpedo nose cones, sonar transducer arrays for ship hulls, and
towed sonar systems.
It was some interesting stuff, but I would have rather been building radar equipment
like was done at the Baltimore division.
Introduction to Ultrasonics
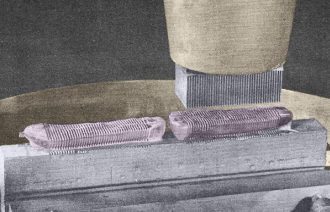
Forty slices of sapphire with one pass of this ultrasonic cutter.
Sound waves, too high in frequency for the human. ears to hear, are vital to
modern industry. They are used to shake, break, weld, boil, cut, grind and clean
By Tom Jaski
Electronics has given modern industry one of the most versatile and most powerful
tools invented by man. It slams molecules of matter against each other to shake,
break, weld, boil, cut, grind and clean. It detects minute flaws or measures the
thickness of an ultrathin sheet of steel with extreme precision. It combines solids
and liquids which nature had never intended as mixtures. It kills germs, cuts through
brain tissue with great precision, sets off burglar alarms and controls television
sets. All this with but one tool, ultrasonic waves.
We have mentioned only a few of its applications. The future will bring many
others, including amplification, detection and communication that will stagger the
imagination.
What are ultrasonic waves? They are waves like sound waves that cause periodic
rarefication and densification we identify in a very limited range as sound, but
they are beyond the range of sound - beyond the normal range of human hearing. Any
sound-like wave above 20,000 cycles qualifies as ultrasonics, including vibrations
up to a frequency of 25,000,000,000 cycles per second (25 kmc ) in solid material
and liquids!
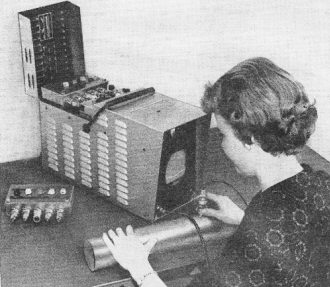
Ultrasonic flaw detection in machine stock. Indentation in scope
baseline indicates a flaw.
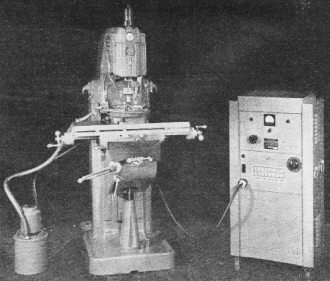
Ultrasonic milling machine.
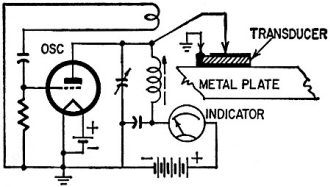
Basic circuit for an ultrasonic thickness gauge.
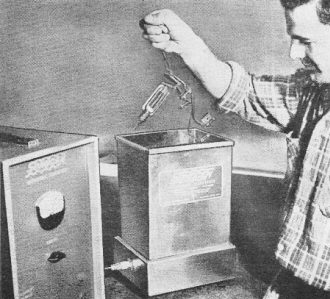
Ultrasonic setup for cleaning miscellaneous metal parts.
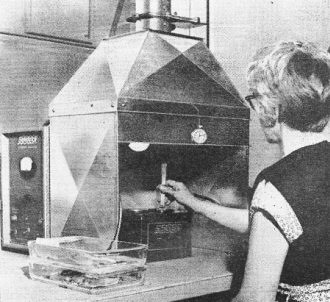
Cleaning small watch parts with ultrasonics. Branson Ultrasonics
Inc. photos
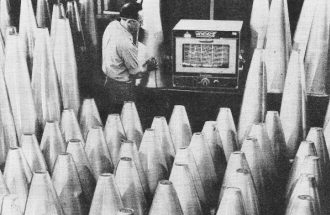
Ultrasonic gauge tests thickness of nose cones for Nike-Hercules
missiles.
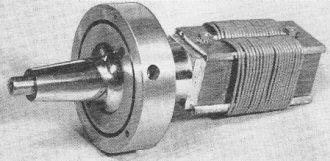
Magnetostriction transducer made by Sheffield.
Experiments with ultrasonics have been carried out for a long time. The versatile
and fantastic genius Sir Francis Galton invented one of the first useful tools for
ultrasonic experiments 100 years ago. He made a Galton whistle, now better known
as a dog whistle. It produces sound waves above human hearing which a dog can perceive.
Of course nature preceded us in our endeavors as usual and provided bats with an
ultrasonic "radar" system so accurate that they can fly in the dark between thin
wires strung only a few inches apart without ever touching them!
How is this tool used in industry? Let us first look into why it is such a powerful
tool. Matter, in spite of what our senses tell us, is mostly space. The molecules
of even the hardest steel are separated by enormous distances compared to the size
of the molecules. And in this space the molecules are in constant random motion.
When we heat a substance, this motion increases, and the hotter we make it the more
the molecules move. If we manage to push some of these molecules around, they will
in turn push on other molecules. It is this transferred push that allows a sound
wave to travel through a substance. The distance between molecules is shorter for
solids than for air and the chance of the molecules colliding with each other is
much greater. This explains why sound travels faster through solids than liquids
and faster through liquids than gases. If we find a frequency which is a submultiple
of the natural frequency of the molecules of the material and shake them up with
it, there is a resonance. The molecules are flung together in some places and torn
apart in others. This is called cavitation. If you have ever seen ultrasonics impinging
on a water bath, you may remember the violent action it evokes!
This wild shaking of molecules can be used in many ways. If we want to mix different
molecules, we just shake them together in lumps and they are soon intermingled thoroughly.
This is emulsification. If the molecules tend to stick together in clusters and
we want to spread them evenly through a solution, we shake them and call the process
homogenizing. If we use an abrasive powder and slam it fast and hard against a piece
of metal, again and again, it eventually chews through the hardest surface. This
is used in ultrasonic grinding and machining. In similar ways we use ultrasonics
for cold welding, cleaning, foaming beer and what have you.
Gauging and measurement is a little different. When the moving molecules in a
dense piece of matter reach the end of that material and find a vacuum or just air,
few of them find gas molecules to push so they bounce back against other molecules
in the solid and start a wave back from the boundary layer. If we adjust the frequency
of the original wave so the time it takes for it to travel out and back is exactly
half a cycle or a multiple of it, we have a 180° phase shift for regeneration.
Any deviation from this precise dimension would immediately show up as an improper
phase shift. The diagram shows the basic circuit of this kind of gauging apparatus.
Flaw detection also uses the back-ward-traveling energy. If we receive the echo
and display it on a scope, flaws show up as extra echoes. Sometimes flaws too minute
to appear clearly in X-rays can be detected with ultrasonics.
When the cavitation we mentioned earlier occurs in living organisms, it literally
tears them apart. Ultrasonic physical therapy does not do similar damage because
the power used is kept low - just high enough to increase the temperature within
the tissue. But the brute force of cavitation tears the most persistent gum and
dirt from parts and equipment in ultrasonic cleaning.
How do we get the energy from the oscillator into the material? It is done with
a variety of transducers. Early equipment used magnetostriction transducers exclusively.
They depend on the fact that a nickel or nickel-alloy rod, when magnetized and subjected
to an AC magnetic field expands and contracts minutely in the field. The expansions
and contractions take place at the rate the magnetostriction rod is resonant to,
determined by its length and material. Magnetostriction transducers are still widely
used, particularly in high-power applications such as machining.
Piezoelectric transducers, such as quartz crystals, have also been used extensively
but they are expensive and limited to relatively low-power applications. But new
ceramic transducers (barium titanate) not only handle more power but are made in
all kinds of useful shapes. One such is a paraboloid which can form the entire bottom
of a cleaning vessel, concentrating maximum energy in one spot, the focus. For unlike
the longer sound waves, ultrasonic waves can be focused easily, and the higher the
frequency the sharper the focus.
Frequency varies all over the lot. The spectacular 25,000 mc cited earlier was
generated by General Electric scientists in their laboratory. They expect to use
it to investigate subatomic forces. Practical industrial frequencies range from
20 kc to 25 mc, with the majority of applications in the 20-100-kc region. This
is where most of the cleaning, homogenization, emulsification, pasteurization, etc.
takes place. However, cleaning small parts is done at frequencies up to several
megacycles. Frequencies lower than 20 kc are rarely used. Most human hearing is
limited to 16 kc, but a few individuals, particularly young women, can hear 20-kc
signals. To be in the vicinity of an 18-kc ultrasonic cleaning bath would be sheer
torture to such a person.
What are the advantages of ultrasonics over other methods? In cleaning, the answer
is obvious. Only very thorough and repeated mechanical scrubbing plus highly potent
solvents could do as good a job. Ultrasonics makes rapid, automatic cleaning lines
possible. Flaw detection allows a measure of certainty unheard of by other methods
except X-rays, and is much safer and much more economical to use. Ultrasonic gauging,
depending on resonance as it does, can be far more accurate than mechanical gauging,
and has the advantage over other electronic gauging methods that it can be used
with just about any material.
In machining, ultrasonics can do things that cannot be done any other way. It
can handle materials no other machining methods can touch. For example, ultrasonic
equipment can machine and emboss glass and gem stones, ceramics and hard metals.
It can drill holes through materials which withstand any other attempts at penetration.
In many instances the ultrasonic tool can chew its way through materials in a fraction
of the time that would be required by more conventional tools.
In medicine, ultrasonic waves can reach inaccessible places and be focused with
pin-point accuracy on tiny spots in the brain or other parts of the human body to
perform minute knifelike operations. Delicate, complex and precise shapes that open
up new discoveries, new scientific instrumentation physically impossible before,
can be fashioned with ultrasonic tools.
And we have only seen the beginning. Ultrasonic burglar alarms are in use in
banks. Ultrasonic washing machines for the home are feasible, though not yet economical.
The future will bring a great many new applications for this versatile tool which
is already making a substantial contribution to industrial technology and scientific
development today.
Posted February 2, 2023
|